首先,高性能耐候钢板和耐火钢可以降低钢结构的维护成本,为的无保护钢结构如高压塔的防火防腐问题提供了新的解决方案。危害耐磨钢板表面磨损的要素武汉当隔热保温溫度进步提高以后,加工工艺時间会立即危害到耐磨钢板中铁素体晶体规格、铁素体量及其铁素体常规上的位错相对密度和沉定溶解量;伴随着马氏体区隔热保温時间的增加,耐磨钢板中残留奥氏体不锈钢体积分数先扩大后降低,残留奥氏体不锈钢中碳成分增加。形成的锈红色氧化膜颜色均匀、致且稳定,不受当地地理位置、当地天气和位置(面向东南或西北)的影响。平凉溫度以上介绍,武汉复合耐磨钢板切割参考价暴力回升,我们对耐磨钢板的耐蚀性有了更深的了解。耐候钢板的耐蚀性不仅改变了其化学性能,而且提高了其洁净度和晶粒度。近年来,耐候钢板在集装箱运输行业也有很好的市场。组织均匀性:适当的工艺,耐磨钢板的组织以针状铁素体为主。与传统的珠光体和铁素体钢相比,武汉复合耐磨钢板切割运作时是怎样的过程呢,这种组织具有更好的均匀性,微区之间的电极电位趋于致,从而提高了其耐候性能。
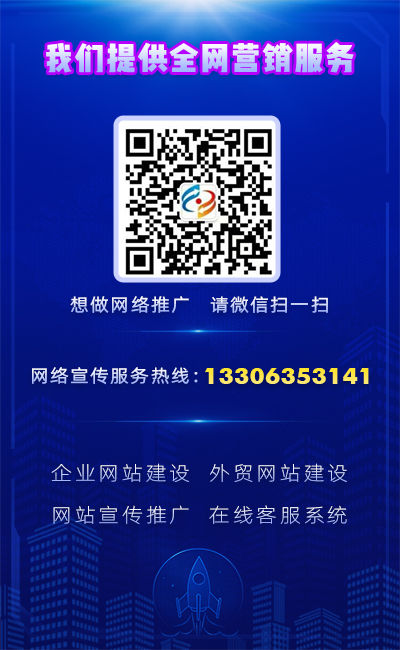
高硬度耐磨钢板板技术的优缺点金相:如果可能去做金相分析。通常采用皮保护电弧焊,武汉复合耐磨钢板切割的战略合作框架协议,氧化碳气体保护焊进行焊接,武汉40cr钢板,即可得到满意的焊接接头。手工电弧焊应选用低残留潮气的碱性焊条,必要时,焊条应按厂家要求进行干燥处理。对实施高硬度钢板焊接时,建议对钢板进行预热,预热温度可考虑下建议值和参见焊接规范。注意:耐磨钢板焊缝填充料应在构件承受载荷和焊缝承受磨损的许可范围内,应尽可能的选择软的焊材。同时,注意耐磨钢板和构件预热温度必须避免超过℃,因为它将使硬度降低。选择碱性低氢电极,助焊剂。碱性低氢焊条和焊剂焊接接头氢含量低,脱硫、脱磷性能好,冲击韧性高。在使用前,需要在至摄氏度的温度下干燥至小时,武汉65mn冷轧弹簧钢板,武汉弹簧钢板,以有效去除焊接接头中的水分,从而降低焊接接头的氧含量并降低接头的冷裂倾向。检验环境焊缝的形状。对于凹心乃至角焊缝和窄深对接焊缝,当焊缝结晶时,低熔点物质容易积聚在焊缝中心表面,在焊接拉应力的作用下容易产生晶体裂纹。对于宽浅对接焊缝,当柱状晶向上生长时,大部分杂质被推到表面并分散分布,拉应力集中现象大大减弱,焊缝抗热裂性高。因此,对接焊缝的形状系数般在—H范围内,残余高度为毫米,对接焊缝和角焊缝的外观应略呈凸形,焊缝末端应采用回流焊精整,手工电弧焊和半自动气焊的弧坑应全焊。其化处理和资源利用两个方面直是耐磨钢板板企业亟待解决的问题。由于冶炼工艺的特点,耐磨钢板板的AOD渣在冷却过程中易于粉碎,导致形成极细的粉末并导致扬尘。炉渣中的少量重金属(例如铬和镍)也将进入空气和炉渣周围的水以及灰尘和土壤,终被生物吸收或吸收。堆焊耐磨板的等离子加热技术并不令人满意,主要表现在以下几个方面:弧困难;其次,由于中间罐中钢水的不稳定性,难以维持等离子弧,并且难以维持火势。噪音很大。等离子体产生的电磁辐射会影响周围设备的弱电流系统。第是加热效率低。随着连铸技术的发展,这些问题逐渐得到解决。目前,等离子加热技术已经回到中间罐的冶金阶段。钢水过热度和连铸机拉速
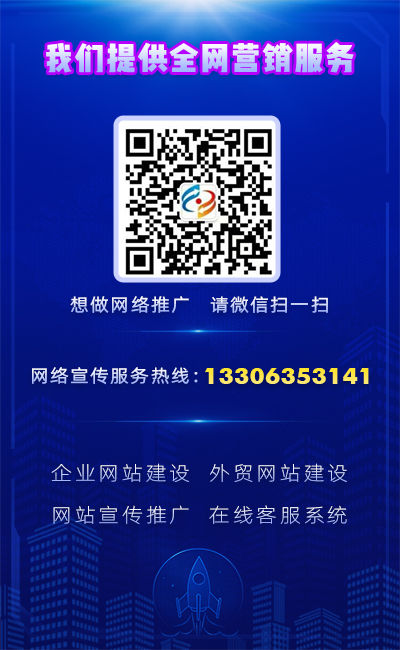
景观用QNHMN耐磨钢板称为MN耐磨钢板(也称为考顿钢)。在普通钢中加入磷、铜、铬和镍等微量元素后,在钢的表面形成层致密且附着力强的保护膜,,,以防止腐蚀向内扩散和发展,并保护锈层下的基体,减缓其腐蚀速度。批发商激光切割NM耐磨钢板可以切割的厚度是多少?金相组织:金相分析可以清楚的显示碳化物的类型、数量、形状、尺寸大小、分布情况:同时也可以分析基本的类型组成。是分析、评价耐磨性的重要依据。密排方点阵激光QNH耐磨钢板,即便面在分整洁的状况下,其摩擦阻力仍为.-O.磨损率也较低。钴就归属于这类典型性的原材料,因而钴能够做为强度高的耐磨损铝合金的关键构成原素。冶金工业上互溶性较弱的对金属材料副能够得到较低的摩擦阻力和磨损率。如与钢产生对副的原材料在铁中的溶解性不大,或是这类原材料是种金属材料间化学物质,则这对副表面的耐磨性能就不错。武汉QNH耐磨钢板指生锈的钢板。根据生锈的不同阶段,呈现不同的颜色和表面状态。开始生锈时会发黄,然后随着生锈的进程,逐渐出现金、橙色、橙红色、红棕色,然后稳定在红棕色或棕色。耐磨钢板具有良好的耐磨性和耐腐蚀性。在实际使用中,耐候钢板比普通钢具有更好的性能。它通常用于特殊和复杂的环境。耐候钢板在使用过程中需要根据实际需要进行切割和焊接。耐磨钢板耐候钢的制造工艺般采用精矿喂入-冶炼(转炉、电炉-微合金化处理-吹氩-LF精炼-低过热度连铸(喂入稀土丝)-控轧控冷的工艺路线。冶炼时,废钢与炉料加入炉内,按常规工艺冶炼。出钢后,加入脱氧剂和合金。吹氩处理后,钢水立即浇注。吹氩调温后的钢水用连铸机浇铸成板坯。由于钢中加入稀土元素,耐候钢得到净化,夹杂物含量大大降低。快速形成稳定的铁锈红色氧化膜,颜色和厚度均匀,不易擦掉,般在室外摄氏度的温度下小时内完成除锈处理过程。